micropillar compression test|Micropillar Compression : store Micropillar compression test was introduced by Uchic et al. (2003, 2004). The focused ion beam (FIB) machining is used to fabricate nano to micron sized metallic pillars. Accordingly, the effects of pillar size can be investigated using micropillar compression test. They observed that . 10. 11. 12. 677 bucetuda FREE videos found on XVIDEOS for this search.
{plog:ftitle_list}
Resultado da 7 de dez. de 2023 · Baixe e ouça grátis o novo CD de arrocha de Nadson O Ferinha, lançado em 2023. O CD contém 14 músicas, incluindo o .
Micropillar compression test was introduced by Uchic et al. (2003, 2004). The focused ion beam (FIB) machining is used to fabricate nano to micron sized metallic pillars. Accordingly, the effects of pillar size can be investigated using micropillar compression test. They observed that .Strain hardening is a process to promote the metal harder and stronger due to .
Fig. 1.6 shows evolution of displacement and load as a function of time as .Micropillar compression testing is a novel method for investigating the mechanical .Microcompression testing became an incredibly popular approach to .
Micropillar compression testing is a novel method for investigating the mechanical properties of materials at small length scales, including CRSS, elastic modulus, fracture .Compared with conventional instrumented indentation (e.g., nanoindentation), the microscale compression test of a geometrically defined pillar has the obvious advantage of a relatively .
Bittencourt, E, Interpretation of the size effects in micropillar compression by a strain gradient crystal plasticity theory. International Journal of Plasticity , 2019 . 116 : 280 – 296 .
The micro-pillar compression test is emerging as a novel way to measure the mechanical properties of materials. In this paper, we systematically conducted finite element analysis to evaluate the capability of using a micro-compression test to probe the mechanical properties of both elastic and plastic materials. We found that this test can provide an . where D Pillar is the micropillar’s diameter, D the diameter of the particle, σ Sub the uniaxial, compressive yield strength of the substrate, and σ Pillar is the yield strength of the pillar. Equation 1 is derived by equating the load required to the yield the pillar (uniaxial compressive yield) with the load needed to yield the epoxy substrate (multiaxial contact yield), . Micropillar compression tests were carried out ex situ (Hysitron Triboindenter TI950 system) and in situ (Hysitron PI88 system) within the SEM. It was reported previously that size effects on the flow stress for different deformation modes (basal and pyramidal slip as well as twinning) were minimum in Mg and Mg alloys for micropillars of these .
The raw data obtained during micropillar compression are presented in Figure 5, serving as a representative curve for the micropillar compression test. Noteworthy is the initial curve data, depicted in the blue shaded region, indicating a slower rate of load increase with displacement, suggestive of roughness alignment with the flat micropillar .
Micropillar compression tests in a scanning electron microscope, microindentation and macroscopic compression tests were performed on dry ovine bone to identify the elastic modulus, yield stress . In situ micropillar compression and nanoindentation were performed on photolithographically fabricated SU-8 polymer inside a scanning electron microscope (SEM), covering seven orders of strain rates from 10-3 to 10 3 s −1.The extracted mechanical properties – modulus, hardness, yield strength, strain rate sensitivity (SRS) exponent – were systematically . Ultra-small testing technologies (USTTs), such as nanoindentation hardness tests and micropillar compression tests, can be potentially used to measure the mechanical properties of irradiated materials. However, the hardness and yield strengths of USTTs are different from those of standardized methods on bulk samples. The micro-scale deformation behavior of the coatings was explored through micropillar compression test. Fig. S3 shows the micropillar structures of TiAlN-0SALand TiAlN-2SAL samples, measuring φ1.2 × 3.6 μm and featuring multiple sublayer structures. The observed deformation behavior during compression was the result of the combined action of .
Although the micropillar compression test was developed as a counterpart of nanoindentation for measuring elastic constants such as the modulus of elasticity, there are a number of experimental works in the literature that report stress-strain curves of micropillar compression tests of various materials showing a discrepancy between the initial .
We measure the yield stress and elastic modulus from each micropillar compression test. A finite element model provides a two-dimensional visualization of the development of plasticity through the pillars and their base material. Finally, TEM and atom probe tomography characterize the irradiated microstructures, which correlate well with the . Single-crystal micropillar compression test has been proven to be an effective method to investigate the mechanical properties of hard and brittle materials, such as Laves phases [[11], [12], [13]], oxides [[14], [15], [16]] and aluminides [17, 18]. This method is usually performed though pressing micrometer or submicrometer-sized pillars . Bittencourt, E, Interpretation of the size effects in micropillar compression by a strain gradient crystal plasticity theory. International Journal of Plasticity , 2019 . 116 : 280 – 296 .
The micropillar compression test is a novel experiment to study the mechanical properties of materials at small length scales of micro and nano. The results of the micropillar compression .
Micropillar compression of single crystal tungsten carbide, Part 1: Temperature and orientation dependence of deformation behaviour. . Appendix – lattice rotations from mechanical constraint during micropillar compression. During a compression test, the pillar is mechanically constrained by the rigid flat-punch indenter face on top of the .
In this study, the effect of hydrogen on dislocation and twinning behavior along various grain boundaries in a high-manganese twinning-induced plasticity steel was investigated using an in situ micropillar compression test. The compressive stress in both elastic and plastic regimes was increased with the presence of hydrogen. Further investigation by transmission . The compression behaviors of iridium single crystals with different crystalline orientations were investigated by micropillar compression tests and molecular dynamics (MD) simulations. The results indicated that the deformation process of iridium single crystals with [100] and [110] orientations was presented as the stacking faults expansion and the formation of . (a) Representative engineering stress-strain curves of micropillar compression tests in micropillars carved from grain B. The black starts indicate the yield point in each curve.
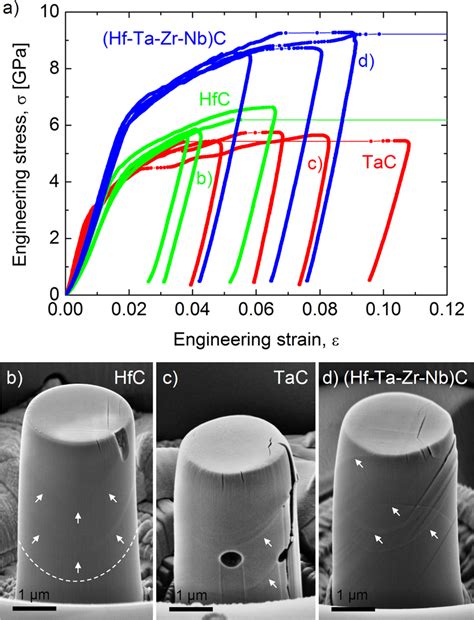
Preparation and compression test of micropillar. After obtaining the gradient lamellar microstructure, micropillar samples were prepared at different depths with different lamellar thicknesses on the cross-section of the Ni rod. The equipment used to prepare micropillar samples is a Zeiss Crossbeam 340 focused ion beam (FIB) and scanning . ABSTRACT. Micropillar compression experiments show size effect, σ p /μ = A(d/b) n, where σ p, is the flow stress, μ is the resolved shear modulus, d is the pillar diameter and b is Burgers’ vector. With fcc metals n ≈ –0.67 and A ≈ 0.7; however, with bcc metals there is greater variation, with n closer to zero. Here we propose a different but similar empirical . Cylindrical micropillar compression test was conducted by FIB milling to identify the mechanical properties of the coating under deformation. The stress-strain curves demonstrated that an ultrahigh compressive strength of 5.3 GPa with strain beyond 12.5% was surprisingly achieved for Cr 2 AlC coating, which was 5 times larger than all the .
The micro-pillar compression test is emerging as a novel way to measure the mechanical properties of materials. In this paper, we systematically conducted finite element analysis to evaluate the . Example of a micropillar compression test on a micropillar built from a multilayer stack of different coatings. Outlining Micropillar Compression Testing. In a typical micro-compression test, a micrometer-scale (μm) pillar of sample material is compressed in a nanoindenter with a calibrated flat punch probe rather than a tip with a pyramidal . These results provide new insights to optimize the specimen size for the micropillar compression test applied for the 18Cr ferritic stainless steels. (a) Optical micrograph and (b, c) SEM images .
Micropillar Compression
2.2. High dynamic micropillar compression tests Micropillar compression tests were conducted using an ALEMNIS in-situ nanoindenter apparatus in a Zeiss Gemini supra 55VP Scanning Electron Microscope (SEM). The test consists in compressing a small pillar with an instrumented diamondflat-punch to extract the local load-displacement curve. The .
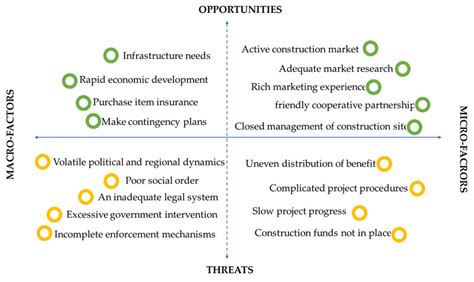
In situ and ex situ micropillar compression tests on single crystals with different orientations were carried out. The stress-strain curves were analyzed in combination with scanning electron microscopy (SEM), TEM and transmission Kikuchi diffraction (TKD) to ascertain the influence of Ca and Zn on the CRSS for slip and twinning. Ultra-small testing technologies (USTTs), such as nanoindentation hardness tests and micropillar compression tests, can be potentially used to measure the mechanical properties of irradiated .
sources of error in vickers hardness test
sources of error in water hardness testing
[Intro] G G C Cm G G Am D G Em A D G Em A.ve Mari.a mãe abençoada virgem imaculada És santa A D D° Am C° G C Semente do amor Maria mãe de Deus És cheia .
micropillar compression test|Micropillar Compression